Technical overview
Coal is usually used as fuel in power plants and industrial boilers, which will produce harmful substances such as sulfur dioxide during combustion. Limestone gypsum wet flue gas desulfurization process is widely used in large coal-fired boilers to remove sulfur dioxide from flue gas. The limestone gypsum wet flue gas desulfurization device produces a large amount of gypsum slurry during operation. The gypsum slurry is composed of gypsum with a certain concentration, unreacted limestone particles and about 80% water. Removing water from the desulfurization gypsum slurry is an important process for desulfurization gypsum treatment. In the traditional device, the dehydration of gypsum slurry is usually completed by the hydrocyclone and vacuum belt conveyor dehydration system, and the water content of gypsum after dehydration is generally about 10%. The traditional FGD gypsum dehydration process system is complex and needs professional gypsum dehydration building, and has high requirements for hydrocyclones and vacuum belt conveyors, which are prone to blockage, wear and corrosion. In traditional devices, hydrocyclones and vacuum belt conveyors are generally imported products, which makes equipment investment costs and operation and maintenance costs higher. At the same time, hydrocyclones and vacuum belt conveyors consume more electricity.
In limestone/gypsum wet desulfurization, vacuum belt dehydrator is used to dehydrate gypsum slurry. This not only reduces the secondary pollution after desulfurization, but also can be used as raw materials for building materials after dehydration. After primary and secondary dehydration, the moisture content of 10% - 15% gypsum slurry discharged from the absorption tower will reach below 10%. The primary dewatering system is mainly a hydrocyclone. The water content of gypsum slurry passing through the hydrocyclone is generally about 50%, which cannot be discharged directly. It must pass through the secondary dewatering system, and after the water content is reduced to below 10%, it can be sold as raw materials for building materials.
In the whole two-stage dehydration system, the vacuum belt dehydrator is the core of the whole two-stage dehydration system. Its working principle is:
The pressure difference between the upper and lower surfaces of the filter cake is formed by vacuum pumping, and the water is squeezed out to achieve the purpose of dehydration. In general, there are certain requirements for the Cl ‐ content of gypsum filter cake, so filter cake flushing water is used to flush filter cake while dewatering to achieve the effect of Cl ‐ flushing.
During the operation of secondary dehydration, the following problems will be encountered.
1) Filter cloth deviation rectifying device failure
The vacuum belt dehydrator and the filter cloth rectifying device failed for a long time and the protection could not be put into operation, which caused the tear of the filter cloth of the vacuum belt dehydrator and the frequent tripping of the vacuum belt dehydrator.
2) Abrasion of adhesive tape
The belt between the belt of the vacuum belt dehydrator and the belt support platform is worn. The ground rubber powder of the belt can be seen everywhere in the water receiving channel on both sides of the belt support platform. The worn rubber strip will block the water receiving channel, and also block the lubrication tank of the support platform, resulting in belt friction and increased resistance, which seriously affects the service life of the belt.
3) Water leakage
Water leakage of the vacuum belt dehydrator causes water accumulation on the ground of the desulfurization gypsum dehydration building. The main leakage parts of the vacuum belt dehydrator are the leakage of the sealing water of the vacuum box and the water receiving tank on both sides of the belt support platform.
4) Scaling of vacuum pump
Desulfurized gypsum vacuum belt dehydrator relies on the vacuum pump to suck out the water in the desulfurized gypsum slurry, so as to achieve the purpose of secondary dehydration of gypsum. Frequent blocking of the operating vacuum pump directly affects the normal operation of the gypsum dehydration system
5) Filter cloth fault of vacuum belt conveyor
After the filter cake flushing water of vacuum belt dehydrator enters the flushing tank, sediment will be generated. During operation, the vacuum pump cannot operate normally due to pipeline blockage.
6) Flushing nozzle blocked
When the content of gypsum in the return water of the filter cloth washing water is high, it is easy to block the nozzle of the filter cake washing water. If the filter cloth is not cleaned for a long time, gypsum will be deposited on the surface of the filter cloth. The filter cloth surface will be blocked, and gypsum will be deposited on the surface of the filter cloth, making it difficult to clean and easy to scale on the surface of the filter cloth,
7) Engine seal failure
The poor sealing performance of the host will lead to the low vacuum degree of the whole system, and the water content of the dehydrated gypsum filter cake is significantly higher, affecting the filtering effect.
8) Degumming of vacuum chamber butt joint
The vacuum chamber is generally made of high molecular polymer. This material has strong expansion and deformation. If it is not fixed in time or is not fixed well, it is easy to cause the vacuum chamber to degumme. In this case, only after stopping the vehicle, put down the truth chamber to re glue and fix each section of the vacuum chamber.
9) Leakage of vacuum chamber flange
There is usually a whistle at the flange connection below the vacuum chamber for leakage. To solve this problem, just stop the vehicle and put down the vacuum chamber to check the gasket. If there is a problem with the gasket, replace the gasket. If it is not a problem with the gasket, only tighten the flange at the leakage.
10) Leakage of filtrate main
Only tighten the leaking bolt. If there is a problem with the gasket, it is necessary to stop the vehicle and replace the gasket.
11) The filter cloth is blocked due to improper operation
If the filter cloth is not cleaned in time, gypsum will scale on the surface of the filter cloth, silting up the surface space of the filter cloth, making it difficult to clean in use, shortening the service life of the filter cloth and affecting the filtering effect.
Generally, the filter cloth needs to be replaced when it is used for more than 12 months, because the filter cloth will deform and shrink after a long time of normal use; In addition, the impurities of the treated materials remain in the filter cloth and cannot be washed away. Although the filter cloth is not damaged, it has seriously affected the filtering effect
12) Belt deviation
Belt deviation is a common problem of vacuum belt conveyor and the most difficult problem to solve. A domestic power plant once imported two vacuum belt dehydrators, and one of them was basically out of service due to belt deviation.
When the belt deviates to a certain extent, the system will automatically stop in an emergency. The reason is that the belt butt joint is faulty. This is the most serious problem in belt deviation, mainly including miter joint and bell mouth. In case of this problem, it is impossible to take other methods to eliminate this error except to replace the belt with a new one.
13) Filter cloth deviation
Filter cloth deviation is also a common problem of vacuum belt conveyor. Filter cloth idling, filter cloth deviation, filter cloth carrier roller displacement.
14) Low vacuum
When this problem occurs, it can be seen from the central control room that the vacuum degree of the whole system is low, and the water content of the dehydrated gypsum filter cake is obviously high.
15) High vacuum
The vacuum degree is beyond the normal range, and the system without mist eliminator flushing device is likely to occur. When this problem occurs, if the problem is not solved in time, the system will automatically stop when the vacuum exceeds a certain degree. The main reason for this problem is that the demister on the gas-liquid separator is blocked by gypsum.
16) The vacuum degree changes periodically
When this problem occurs, the dehydration efficiency also changes periodically with the change of vacuum degree. The dehydration rate increases when the vacuum degree is high, and decreases when the vacuum degree is low.
In general, this problem is mainly caused by the degumming of the filter cloth butt joint.
17) Insufficient dewatering efficiency
The dewatering efficiency cannot reach the standard: first, there is no problem with the vacuum degree, and the dewatering efficiency still cannot meet the requirements when the given materials can completely cover the belt grooving section, and the slurry at the outlet of the hydrocyclone cannot reach the concentration of about 50% required by the belt dehydrator. Second, the vacuum degree is slightly high, but it is not enough to stop, but the dehydration efficiency is still not up to standard. The sludge in the slurry is covered on the filter cake to form a dense layer of sludge, which insulates the gypsum filter cake and air, and the water in the filter cake cannot be squeezed out.
18) Cl ‐ in filter cake exceeds the standard
Cl ‐ content in filter cake is an important indicator for detecting desulfurization system. Generally, the dehydration rate is concerned. In order to achieve the dehydration rate, the supplier will also deliberately reduce the amount of filter cake washing water, resulting in the excessive Cl ‐ content in the filter cake.
19) The filter cake flushing water pipe and nozzle are blocked
Generally speaking, because the filter cloth washing water is process water, it will not be blocked. The gypsum content in the filter cloth washing water return water is relatively high, so it is easy to cause blockage of the filter cake washing water nozzle.
20) Filter cake thickness is too thick or too thin
The filter cake is too thick, which will result in insufficient dehydration efficiency; If the filter cake is too thin, it will cause local leakage, and the dehydration efficiency may not reach the standard.
21) Uneven blanking
Uneven blanking phenomenon is shown as follows: the whole filter cake is uneven in longitudinal shape, and there are obviously protruding long filter cakes. The reason for this is that the baffle effect of the feeding device is not good enough.
Some filter cakes have a thickness of more than 100mm, and there is a hidden danger in the dewatering efficiency of too thick filter cakes.
2、 Desulfurization gypsum slurry dehydration Solid-liquid separation Complete technology
The complete set of desulfurization gypsum slurry dehydration solid-liquid separation technology is to solve the problems of high process energy consumption, easy blockage, easy water leakage, easy corrosion, high power consumption, high maintenance workload, and high operating costs of the traditional desulfurization gypsum vacuum belt dehydrator, and to reduce power consumption, equipment investment, operation and maintenance costs, and the cost of coal-fired boiler flue gas desulfurization project, To further improve the desulfurization efficiency, a new complete set of solid-liquid separation technology is proposed. Compared with the traditional desulfurization gypsum dehydration process, this technology optimizes the wet desulfurization gypsum process, reconfigures the desulfurization gypsum dehydration unit and its process flow, equipment selection, and process layout, Complete the dehydration of desulfurization slurry with low energy consumption, replace the traditional gypsum vacuum belt dehydrator, and solve the problems and drawbacks of the traditional gypsum belt dehydrator. The whole process is a physical process, without chemical reaction, without hydrocyclone and vacuum belt conveyor, which is not easy to block, wear, and corrosion, It eliminates the hydrocyclone and vacuum belt of the traditional vacuum belt dehydrator dehydration system, reduces the power consumption of the system, reduces the equipment investment costs and operation and maintenance costs, reduces the cost of flue gas desulfurization projects, improves the flue gas desulfurization effect, and is widely applicable to the limestone gypsum wet desulfurization gypsum dehydration process.
3、 Complete set of solid liquid separation technology for desulfurization gypsum slurry dehydration
Desulfurized gypsum slurry dewatering solid-liquid separation complete technology is a new technology for desulfurized gypsum slurry dewatering solid-liquid separation. It is a substitute for the traditional desulfurized gypsum slurry dewatering filter. It has broad market prospects. It is a national and key product, and has applied for 10 projects Invention patent It is used for dehydration of desulfurized gypsum slurry and solid-liquid separation, and has obtained obvious economic benefits. Its energy consumption is only 10-20% of that of ordinary filters. It is known as a milestone technological progress in solid-liquid separation and filtration industry. In China, desulfurization gypsum slurry dehydration solid-liquid separation field has been widely used. Features: less investment, quick effect, high efficiency, low operating cost, simple operation, convenient use, which is incomparable to any old filtering equipment. This technology does not need a hydrocyclone and a vacuum belt conveyor, and it eliminates the hydrocyclone and vacuum belt of the traditional dehydration system. Under the condition of occupying a small area and building volume, the dehydration of desulfurization slurry is completed with low energy consumption. The whole process is a physical process without chemical reaction, which is not easy to block, wear, and corrosion. The separated water is like tap water, which can be recycled to save a lot of water resources and improve economic benefits. The separated gypsum has a moisture content of about 10%, good looseness, and can be stored, transported, and used easily. It does not need a dryer to dry, and can be used for building materials, reducing system power consumption, equipment investment costs, operation and maintenance costs, and reducing the engineering cost of the desulfurization system, The effect of flue gas desulfurization is improved, and the gypsum dehydration process is suitable for the limestone gypsum wet flue gas desulfurization process.
4、 Complete set of solid liquid separation technology for desulfurization gypsum slurry dehydration
The complete set of solid liquid separation technology for desulfurization gypsum slurry dehydration is an advanced technology Solid liquid separation equipment It has high efficiency and energy saving, and is suitable for petroleum, chemical industry, electric power, metallurgy, building materials, black and non-ferrous metal beneficiation, fine pulverized coal, food, sewage treatment and other fields. This technology is a solid-liquid separation equipment designed by using vacuum negative pressure and the capillary effect of microporous silicon carbide materials to achieve filtration, and using the capillary principle of micropores - permeability and impermeability, The diameter of micropores is generally 0.1-10 μ m. The micropores of the filter plate are small and transparent to each other. The filter uses hydrophilic microporous filter disc as the filter medium. When filtering, the micropores in the filter disc have capillary effect in the gypsum slurry. Under negative pressure, the surface tension between the hydrophilic filter plate and water can prevent the water in the micropores from being completely evacuated, and the water in the micropores can prevent the air from entering, Therefore, only a small power of vacuum pumping equipment is needed to obtain a higher vacuum degree close to the low altitude used. Its installed power is only 10% of that of traditional filters, which is very energy-saving. During production and use, the filter cake is adsorbed on the surface of the filter plate, and the filtrate is sucked away through the micropores of the filter plate. This process circulates back and forth to achieve the purpose of solid-liquid separation. It has the advantages of advanced technical performance, energy conservation and consumption reduction, cleanness and environmental protection. It is a replacement product of the traditional cloth filter with high energy consumption. It can replace imported and traditional filters. It can filter by using the pressure generated by compressed air (or compressed air and vacuum suction at the same time), which can increase the pressure difference by nearly 10 times compared with ordinary filters, greatly improving the production capacity of the filter, Reduce the moisture content of filter cake, realize one-time solid-liquid separation, reduce the operating cost of the filter, and improve the adaptability of the filter to materials.
5、 Principle of Complete Set of Solid Liquid Separation Technology for Gypsum Slurry Dehydration
The unique principle of the complete set of gypsum slurry dehydration solid-liquid separation technology is based on a natural phenomenon, that is, when a very thin pipe is immersed in water, the water surface in the pipe will be higher than the water surface around it, making the small pipe holes have a lifting force, which is caused by the surface tension of water and the affinity between pipe walls. On the contrary, if the thin pipe is lifted out of the water surface, it will not flow out. Only the gas with a certain pressure can blow out the residual water in the tube. The capillary tube has two functions, one is to draw water into the tube, the other is to keep the water in the tube and prevent air from passing through the thin tube.
6、 Complete technical performance of gypsum slurry dehydration solid-liquid separation
Gypsum slurry dehydration Solid liquid separation technology It is based on this principle that the filter with silicon carbide as the basic component is covered with a diameter of less than 2 μ M holes, each of which is equivalent to a capillary tube. After this filter medium is connected with the system, when water is poured onto the surface of the filter piece, the liquid will pass through the micropores until all free water disappears. Thereafter, no liquid will pass through the medium, and the water in the micropores will prevent the passage of gas, thus forming a filtration process without air consumption, This is also the reason why gypsum slurry dehydration solid-liquid separation equipment can save energy compared with other filters.
When the filter piece is inserted into the gypsum slurry, the situation is the same as that in water. The water contained in the filter cake is pumped out through the capillary tube (and a small vacuum pump) in the filter piece, and finally reaches the equilibrium state, which is the lowest water content of the filter cake. During this filtering process, the vacuum degree can reach more than 95%, thus maintaining the best filtering state.
7、 Gypsum slurry dehydration solid-liquid separation process
The complete set of gypsum slurry dehydration solid-liquid separation equipment consists of the following parts: gypsum box, mixer, cylinder, pipeline and PLC programmable controller. The structure is compact. All relevant equipment, including vacuum pump, are installed on the filter, and only one filter pump is installed below 3m. Therefore, the gypsum slurry dehydration solid-liquid separation complete equipment only needs a very limited installation space.
The working mode of the gypsum slurry dehydration solid-liquid separation equipment is similar to that of the ordinary disc filter. The working cycle consists of five parts: gypsum slurry feeding, filter cake formation, filter cake drying, filter cake unloading, and backwashing. The gypsum slurry is injected into the slurry feed tank by the thickener underflow, and the agitator is stirred in the tank to prevent the gypsum slurry from settling, The main shaft drives the filter disc with 12 filter discs into the gypsum box to form a filter cake on the filter disc. The thickness of the filter cake can be adjusted by changing the gypsum slurry level and the rotation speed of the filter disc. After the formation of the filter cake, it enters the drying process. The dried filter cake is scraped off the filter disc through a scraper. It is worth noting that during the peeling process of the filter cake, There is still a layer of filter cake adhered to the filter surface, which will be removed by the backwash water, so as to reduce the wear of filter pieces.
8、 Characteristics of Complete Set of Gypsum Slurry Dehydration Solid Liquid Separation Equipment
Capillary gypsum slurry dehydration solid-liquid separation equipment is similar to the traditional vacuum filter, the main difference is that the silicon carbide filter is used. This fired filter with special structure is full of uniform micropores, which only allows the filtrate to pass through, almost absolute vacuum capillarity. Without external force, the disc immersed in the gypsum tank begins to dehydrate by capillary action. The solid in the gypsum slurry stays on the surface of the disc. As long as there is free water in the solid, the dehydration will continue. Only one small vacuum pump is used in the filtration system to increase the flow of filtrate.
The complete set of gypsum slurry solid-liquid separation technology is a high-tech product integrating electromechanical, microporous filter plate, automatic control, ultrasonic cleaning, etc. Compared with the traditional vacuum filter, it has the following characteristics:
1) High vacuum degree and low cake moisture.
2) The cleaning solution is clear, almost free of solid substances, and can be directly returned for use or discharged into the water body.
3) The energy consumption is only 10% - 20% of that of traditional filters.
4) No expensive filter cloth is required.
5) Automatic and continuous operation, low maintenance cost, and equipment utilization rate up to 95%.
6) It can ensure even washing of filter cake.
7) The production is pollution-free and the environment is safe.
8) The filter has long service life, easy replacement and low labor intensity.
9) The cost of gypsum slurry dewatering is only 18.8% - 40.1% of that of traditional filters.
10) The equipment has compact structure, convenient operation and maintenance, and small floor area.
11) The filtering operation is carried out continuously under the vacuum degree of -0.080 ~ -0.082mPa. The filter cake has low moisture and high output.
12) The filtrate is pure, solid content<50mg/kg, which can be directly discharged and recycled.
13) The moisture content of filter cake is less than 17%, with good looseness, which can be stacked, transported and used conveniently.
14) Filter plate micropore is only 0.2~10 μ m. It is suitable for filtration and recovery of fine powder gypsum slurry.
15) The whole process is monitored by a microcomputer, which is easy to operate, safe and reliable in operation, and highly automatic.
The working characteristics of the complete set of gypsum slurry dehydration solid-liquid separation technology are that with the increase of feed concentration, the processing capacity gradually increases, and the working condition is good. If the feed concentration is too thin, the surface of the filter plate is easy to form a thin fine mud layer, which hardens the filtering effect. Therefore, trying to improve the concentration efficiency of the thickener and improve the concentration of gypsum slurry plays a key role in the working efficiency of the filter
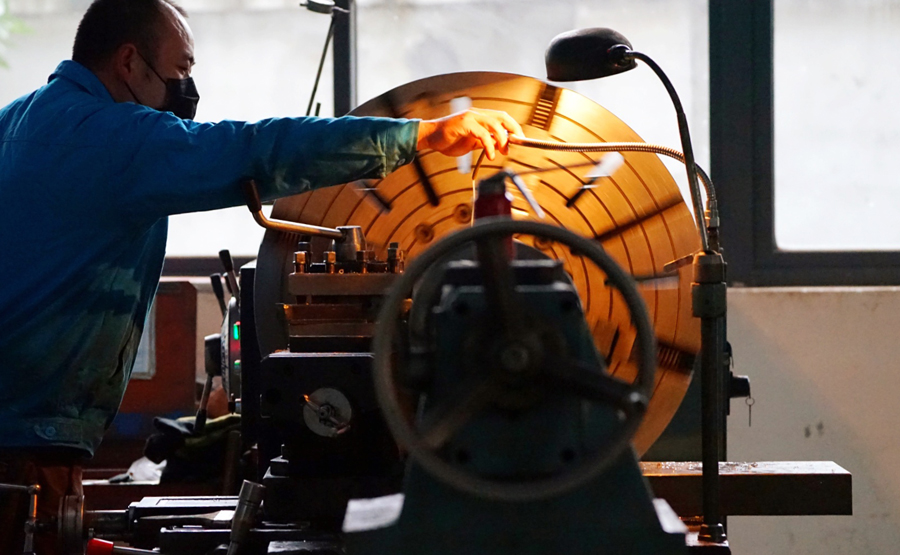
Zhejiang Zhengda Environmental Protection Equipment Co., Ltd.: focusing on Horizontal spiral sedimentation centrifuge, sludge dewatering machine, sludge treatment equipment, centrifugal dewatering machine, sludge dewatering equipment, solid-liquid separation equipment, horizontal spiral centrifuge, centrifuge, mud dewatering machine, mud dewatering equipment, mud treatment equipment, horizontal centrifuge, solid-liquid separator Production, sales and service of various solid-liquid separation equipment. Welcome new and old customers to come for consultation and investigation.
Factory address: No. 812, Jiulong Street, Bihu Town Industrial Zone, Liandu District, Lishui City, Zhejiang Province Telephone: 0578-2788008 Fax :0578-2788681
Email: [email protected] website: //hcsxe.com
Mobile: 15857812218 (Mr. Mao) fifteen billion two hundred and fifty-seven million eight hundred and twenty-six thousand six hundred and nine (Manager Xu) thirteen billion nine hundred and six million seven hundred and eighty-eight thousand three hundred and sixty-seven (Mr. Xu)