China is the largest producer of alumina in the world today. However, bauxite resources in China are not only scarce but also of poor quality. The average alumina silica ratio of bauxite in most mines with industrial mining value is only about 5, which is not suitable for the production of alumina by simple Bayer process (alumina silica ratio>9). Therefore, at present, many alumina plants in China use the combined process of Bayer process and sintering process to produce alumina, that is, first use the improved Bayer process to treat bauxite with an alumina silica ratio greater than 7, then use the sintering process to treat Bayer red mud to recover alumina and sodium oxide (in series), or use the parallel and mixed process of Bayer process and sintering process to produce alumina, There are also those who choose the rich ore sintering method to produce alumina. At present, at least one fifth of the alumina products produced in China come from sintering process. In the future, with the high consumption of bauxite resources year by year in China, the bauxite grade will continue to decline, and the proportion of alumina produced by sintering method will further increase.
The sintering process usually refers to the alkali lime sintering process, which is suitable for the treatment of low-grade (3-5) bauxite. However, the process is complex, energy consumption is high, product cost is high, red mud discharge is large, and environmental pollution is caused. It is urgent to improve and optimize it to adapt to the healthy and sustainable development of China's aluminum industry.
The rapid digestion and liquid-solid separation technology of clinker in sintering process is a key technology to simplify the process flow, save investment, reduce land occupation, reduce energy consumption, improve the recovery rate of alumina and sodium oxide, reduce the alkali content of red mud, and improve the resource utilization level of red mud. However, due to the problem of filter cloth hardening, the slurry dissolved by sintering method has been separated from solid by sedimentation method. Therefore, it is an important research topic to eliminate the filter cloth hardening phenomenon in the liquid-solid separation of sodium aluminate slurry.
1. Hardening phenomenon of filter cloth during liquid-solid filtration separation of sintering dissolving slurry
Filtration is the simplest way to quickly separate the liquid and solid from the sintering dissolving slurry
Leave. Although there are many types of filter models, it is difficult to filter and separate sodium aluminate slurry. The basic reason is that sodium aluminate in the solution is easy to hydrolyze and decompose to precipitate Al (OH) 3 in the process of filtration, that is, the following reactions occur:
(1)NaAl(OH)4﹢aq → NaOH﹢Al (OH)3﹢aq
(2)NaAl(OH)4﹢CO2 → Na2CO3﹢Al (OH)3﹢H2O
These precipitated Al (OH) 3 are easy to accumulate and crystallize on the surface of the filter cloth and in the capillary channels during the suction filtration process, which will cause the capillary channels of the filter cloth to be blocked, and the filter cloth will gradually lose its filtration performance. At the same time, as the filter cloth is used again and again, the crystal constantly fills the space between the braided fibers, finally making the filter cloth hard and unable to filter and separate the sodium aluminate slurry.
2. Previous work on rapid liquid-solid separation of clinker dissolving slurry
Undoubtedly, not using filter cloth is the easiest way to prevent and eliminate the problem of filter cloth hardening. Therefore, what researchers first thought of was to select a filter without filter cloth to separate the slurry dissolved by sintering method.
Zhengzhou Aluminium Plant and Shanghai at the end of 2002 Centrifuge LW530X2270NY is jointly selected by the research institute Horizontal centrifuge The liquid-solid separation test was carried out on the dissolving slurry of sintering clinker. In the test, the treatment capacity of the test prototype reaches 40M3/h, and the average value of suspended solids in the coarse liquor is 1.92g/L on the premise of adding flocculant in the clinker dissolving slurry; The moisture content of red mud thick pulp is 37.12%; The average dissolution rate of red mud alumina is 95.81%. Compared with 92.2% of red mud aluminum oxide in the bottom flow of the same settling tank, the dissolution rate of red mud aluminum oxide is increased by 3.61%. In 2003, Pan Changyue of Central South University and Liu Jinxing of Shandong Aluminum Oxide Plant also conducted similar tests. Although the rapid liquid-solid separation of clinker dissolving slurry was achieved, the average value of suspended matter in the crude liquid was as high as 7.69g/l. In these tests, there were shortcomings such as easy damage of centrifuge bearings, easy wear of feed inlet, easy blockage of slag outlet, easy scarring of cylinder wall, and many maintenance times, It is verified that this kind of equipment is difficult to meet the requirements of large flow, continuous and stable operation in alumina production.
In 2006, "Research on Prevention and Regeneration Technology of Agglomeration of Sintering Dissolved Red Mud Filter Cloth" was listed as one of the main research projects of the national "Eleventh Five Year Plan" scientific and technological research project "Research on High Efficiency and Low Consumption Alumina Dressing and Smelting Technology". The project was jointly tackled by Chinalco Shanxi Branch and Zhengzhou Light Metal Research Institute. The project team carried out industrial tests in Shanxi Aluminum Plant based on a large number of alumina production technology analysis and laboratory research results. In September 2007, breakthroughs were made in industrial trials. The test filter runs continuously for 6 days and develops a set of high-efficiency separation technology, which can increase the net dissolution of alumina in clinker by more than 2%. From 2010 to 2011, Shanxi Aluminum Plant and Shenyang Aluminum Magnesium Design Institute conducted red mud filtration and separation test of large filter (72m2) on the basis of the above research, but the phenomenon of filter cloth wrinkling and deviation occurred during operation, which hindered the continuous operation of the filter. In this study, the caustic solution with high caustic ratio is used to dissolve the aluminum hydroxide on the hard filter cloth. The high temperature of the caustic solution, long digestion time and easy damage to the filter cloth are the main reasons for the relaxation and wrinkling of the filter cloth. In addition, the precipitates in the capillary channels of the filter cloth cannot be completely removed quickly only by digestion, so the online regeneration of the filter cloth is not complete enough. At present, the research is still in optimization.
It is also reported that researchers have tried to use plate and frame filter press, tilting disc filter and filter cloth bag to filter and separate clinker dissolved slurry, but failed to obtain industrial application in alumina production due to hard filter cloth and continuous operation.
3. Study on Eliminating the Phenomenon of Filter Cloth Stiffness
The results of our experiment of soaking the knotted filter cloth in alkaline solution to eliminate the phenomenon of stiffening show that after soaking the knotted filter cloth in a certain concentration of NaOH solution for a certain time, the stiffening condition of the filter cloth will change, but the filtration performance of the filter cloth cannot be completely recovered. This indicates that Al (OH) 3 crystals on the surface of the filter cloth and near the capillary channel mouth have been dissolved, but Al (OH) 3 crystals in the capillary channel have not been dissolved by NaOH solution. In particular, if the filter cloth is soaked for a short time, the hardening condition of the filter cloth will not change much. It can be inferred that the hardening of the filter cloth is mainly caused by the filling of Al (OH) 3 crystals separated from the capillary channels of the filter cloth.
Since NaOH solution with proper temperature and concentration can reduce the hardening of the filter cloth, it indicates that Al (OH) 3 crystals on the filter cloth can be completely dissolved by NaOH, and the Al (OH) 3 crystals in the capillary channel can be dissolved and removed as long as they can contact with NaOH.
It is feasible to dissolve the Al (OH) 3 crystal in the filter cloth by suction filtration with interrupted filtration and NaOH of appropriate temperature and concentration instead of sodium aluminate slurry. However, the continuous operation of the process is destroyed, so the consumption of NaOH solution is large, and a set of heating and thermal insulation NaOH solution storage system is required. If continuous filtration is not interrupted, the method of rapidly dissolving Al (OH) 3 crystal in capillary channel must be considered. In the experiment, we used an ultrasonic cleaning tank to dissolve and wash the knotted filter cloth. It was found that in the NaOH solution with proper temperature and concentration, the knotted phenomenon of the filter cloth can be completely eliminated quickly with the help of ultrasonic, and the filter cloth can recover nearly 100% of its filtration performance.
When the ultrasonic wave propagates in the medium, the solution will produce numerous tiny vacuum bubbles (cavitation). When the bubble bursts, it will produce very strong impact energy, which can break up the solid objects encountered. In addition, the ultrasonic wave has high frequency, short wavelength and strong penetration ability, which is particularly suitable for cleaning the dirt in complex structures and capillary channels. In addition, cavitation can effectively promote chemical reaction, Therefore, the solution washing device with ultrasonic wave is selected to eliminate the phenomenon of filter cloth hardening.
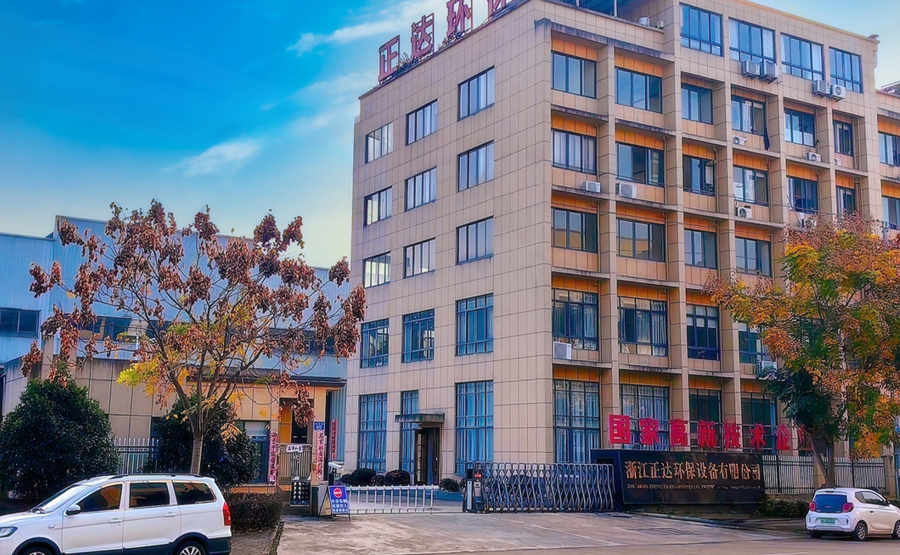
The ultrasonic solution cleaning device is shown in Figure 1, which is mainly composed of a liquid holding tank, an ultrasonic generator, a heating device and a filter cloth guide roller.
When the filter cloth passes through the solution washing tank, it is affected by the alkali solution and ultrasonic wave, and the crystal between the fiber gaps is quickly dissolved into sodium aluminate and then returned to the solution, which achieves the purpose of eliminating the hardening of the filter cloth by solution washing.
This article is written by Zhengda Environmental Protection Equipment Co., Ltd, Horizontal screw centrifuge Manufacturing experts
Zhejiang Zhengda Environmental Protection Equipment Co., Ltd.: focusing on Horizontal spiral sedimentation centrifuge, sludge dewatering machine, sludge treatment equipment, centrifugal dewatering machine, sludge dewatering equipment, solid-liquid separation equipment, horizontal spiral centrifuge, centrifuge, mud dewatering machine, mud dewatering equipment, mud treatment equipment, horizontal centrifuge, solid-liquid separator Production, sales and service of various solid-liquid separation equipment. Welcome new and old customers to come for consultation and investigation.
Factory address: No. 812, Jiulong Street, Bihu Town Industrial Zone, Liandu District, Lishui City, Zhejiang Province Telephone: 0578-2788008 Fax :0578-2788681
Email: [email protected] website: //hcsxe.com
Mobile: 15857812218 (Mr. Mao) fifteen billion two hundred and fifty-seven million eight hundred and twenty-six thousand six hundred and nine (Manager Xu) thirteen billion nine hundred and six million seven hundred and eighty-eight thousand three hundred and sixty-seven (Mr. Xu)