1、 Preface
Horizontal spiral sedimentation type Centrifuge It is a machine that uses centrifugal sedimentation method to separate suspension, and it is used to separate suspension containing fine particles (particle size d ≥ 5 μ m) Suspension, after Solid-liquid separation The suspension becomes relatively clean liquid and solid sludge. Because there is no filter cloth and filter screen, the power consumption per unit output is less, and the production capacity of a single machine is large, which is suitable for the requirements of large-scale and automatic centralized control of the factory. There is no operation cycle, continuous operation, continuous feeding and unloading, simple operation, low solid content of mother liquor, high clarity, and compact structure, It has the characteristics of small floor area and easy sealing, and has been widely used in environmental protection, petroleum, chemical industry, metallurgy, medicine and food, light industry and other fields. The structural diagram is shown in Figure 1, and the main components are drum, screw conveyor differential mechanism Overload protection device and slag unloading device. Its working principle is: in the casing, the drum and the auger are connected by two concentric bearings, the main motor drives the drum to rotate through the V-belt pulley, the drum is connected to the planetary differential housing through the hollow shaft at the left bearing, and the output shaft of the planetary differential drives the auger to rotate in the same direction with the drum, but the speed is different. The suspension is continuously fed into the drum from the central feeding pipe at the right end. Under the action of centrifugal force, an annular liquid pool is formed in the drum. Heavy phase solid particles are centrifugally settled on the inner surface of the drum to form sediment. Due to the relative movement of spiral blades and the drum, the sediment is pushed to the drying area at the small end of the drum by spiral blades, sent out of the liquid surface and thrown out of the slag discharge hole. A number of overflow holes are arranged on the big end cover of the drum, from which the liquid phase flows out, thus completing the solid-liquid separation.
The selection of horizontal spiral sedimentation centrifuge is related to many factors, such as design concept, physical and chemical property parameters of materials and process routes, which should be paid attention to during the selection process.
2、 Design concept
The main technical features of the design of horizontal screw sedimentation centrifuges at home and abroad are basically the same, but there are great differences in the design concept of technical details, mainly in the selection of technical parameters, materials, starting mode, driving mode and differential mechanism.
(1) The main technical parameters of the horizontal screw sedimentation centrifuge are the drum diameter, length diameter ratio, separation factor and screw head number. The larger the drum diameter is, the larger the production capacity is. However, due to the limitation of material strength and processing difficulty, the drum diameter cannot be larger than a certain value. Similarly, the larger the length diameter ratio is, the greater the production capacity is. For materials that are easy to separate, the length diameter ratio is 1~2, and for materials that are difficult to separate, the length diameter ratio is 3~4. Therefore, the machine with large length diameter ratio can be used as far as possible to increase the length of the settling zone and the drying zone, which is conducive to sedimentation and reducing the moisture content of the filter cake, but it is difficult to manufacture and the cost increases. Separation factor Fr= ω 2R/g is directly related to the rotating speed of the drum. Its selection depends on the difficulty of separating the solid particles in the suspension. The rotating speed of the drum is limited by materials and bearings. Therefore, when meeting the use requirements, the rotating speed of the drum should be as low as possible. Generally, large diameter Horizontal screw centrifuge The separation factors are very low. The number of screw heads can be single head, double head and multiple head, and the materials difficult to separate are generally single head screws; For materials with large output and easy separation, multiple heads are often used, but the solid content of mother liquor will increase. In sewage treatment industry, single head spiral is generally used.
In addition, the semi cone angle of the drum and the inner diameter of the overflow port are technical parameters to be considered when designing the centrifuge. The semi cone angle has an important influence on the performance of solid flow. Due to the centrifugal force, when the particles reach the inner wall of the rotating cylinder and are transported forward by the spiral, they also have a backward flow trend. The backward flow speed is related to the spiral bevel angle, which is finally reflected in the cone angle. Both of them have a direct impact on the transport performance of solid particles, that is, the solid transport speed decreases with the increase of reflux speed. The inner diameter of the overflow port is related to the thickness of the liquid layer. The thickness of the liquid layer increases with the increase of the liquid residence time in the machine. The result is that the clarification efficiency is improved, but at the same time, the shortening of the drying interval in the machine will also increase the water content of solids leaving the liquid surface, that is, the dehydration effect is reduced. Therefore, the adjustment of liquid layer thickness will directly affect the settling speed, flow and solid discharge. In order to determine the type and structure of the horizontal screw centrifuge, analysis and research should be carried out according to the use experience and test results.
(2) The strength of materials is reflected in the rotating speed of the centrifuge, which also directly affects the volume flow and mass flow. In addition, the corrosion of the centrifuge is also related to its material structure. The drum and auger are usually cast and welded with stainless steel, or made of high-strength stainless steel and titanium steel, or fiberglass. At present, the main components of domestic and foreign equipment are made of stainless steel, especially the drum and spiral parts are all made of stainless steel. Only a few foreign manufacturers can use appropriate materials for different processing objects and media requirements. For example, for sewage treatment and non corrosive occasions, the use of high-strength carbon steel for corrosion prevention has avoided over design and greatly reduced manufacturing costs. Through more than 10 years of practice, it has been proved that it is completely feasible to use carbon steel for corrosion prevention in sewage treatment. In terms of shell, material saving and cost reduction shall be considered as far as possible, such as using glass fiber reinforced plastic shell. Wear resistance shall be taken into consideration when selecting materials of the drum and spiral. In order to effectively protect the drum, wear sleeve shall be set at the slag discharge hole, and ribs or grooves shall be set on the inner surface of the drum; The blades of the screw conveyor are vulnerable to serious wear of materials. In order to reduce or avoid the wear of the blades, tungsten carbide thermal spraying treatment is carried out on the outer edge of the spiral blades and alloy blocks are welded.
(3) Starting mode Domestic and foreign centrifuge manufacturers have different considerations on centrifuge starting. Foreign machines are mostly equipped with hydraulic couplings, while domestic machines are mostly started directly due to manufacturing technology. The hydraulic coupling has two functions: one is to enable the motor to start with light load, which can improve the starting ability of the motor, ensure that the motor can start with heavy load quickly, reduce the starting current of the motor, achieve soft acceleration, and reduce the impact on the power grid; Second, it has overload protection function, which can effectively protect the motor and centrifuge from damage when starting and overloading, reduce the failure rate of the machine, and extend the service life of parts and the whole machine. The oil filling amount of the hydraulic coupling should have an optimal value. If the oil charge is too full, the starting current will be too high for a long time, causing shutdown. If there is less working fluid in the hydraulic coupling, the slip of the hydraulic coupling will increase, the transmitted power or torque will decrease, making the input speed much lower than the output speed, and the temperature of the hydraulic coupling will increase. In addition, the selection of working fluid is also important. The higher the density of working fluid, the stronger the transmission capacity. The higher the viscosity of the working fluid, the more unfavorable the transfer characteristics. The hydraulic coupling is generally installed with two fusible plugs, and there is a soft soldering in the center of the fusible plug, which will melt at a certain temperature. When the centrifuge is overloaded, the working fluid in the hydraulic coupling will overheat. When the set value is reached, the fusible plug will melt, the working fluid will spray out, the power transmission will be interrupted, and the centrifuge will interlock and trip.
(4) In terms of driving mode, there are great differences between domestic and foreign models. There are many different driving modes for foreign models, while the driving mode of domestic centrifuges is usually single, and the most used driving mode is dual motor structure. Single motor drive mode: a motor drives the drum through the main pulley, and the secondary belt drives the shaft of the differential to generate a differential speed. When adjusting the differential speed, it needs to stop the machine, which is a simple drive mode; Or the differential input shaft is fixed, and the drum is driven by a single motor; Dual motor drive mode: one motor drives the drum directly through the belt to generate rotation, and the other motor drives the screw through the differential. In addition to the commonly used dual motor system drive mode, imported equipment can often provide a variety of drive modes. The commonly used drive mode is hydraulic drive, that is, the drum and screw are driven by independent hydraulic systems, which has advantages that other drive modes cannot compare: greater drive torque, more convenient speed difference control mode, and lower speed difference. The disadvantage of this drive mode is that the equipment cost is high, and the requirements for hydraulic system and electric control system are very high. Because there are many hydraulic connection points, there are more opportunities for leakage. Therefore, this driving mode has strict requirements on the quality and reliability of hydraulic components.
The spiral and drum rotate in the same direction, but there is a speed difference between them. If nb represents the absolute speed of the drum and ns represents the absolute speed of the screw, Δ= Nb ns, if the screw is ahead of the drum, it is the positive differential speed; otherwise, the screw is behind the drum, it is the negative differential speed. The use of positive differential speed is conducive to sedimentation separation, and the use of negative differential speed is conducive to the transport of sediment, and can reduce the power transmitted by the differential. Therefore, modern spiral sedimentation centrifuges mostly use the negative differential low speed right-hand spiral. Different driving modes will eventually lead to different differential speeds. Differential speeds are the key factor affecting the moisture content of filter cakes. Low differential speeds can produce drier filter cakes, and accordingly reduce the wear of the screw, which can greatly extend the service life of the screw. In addition, increasing the differential speed not only increases the solid flow, but also increases the agitation in the clarification area of the machine, thus reducing the clarification efficiency. At this time, the volume flow must be reduced. Increasing the differential speed will also reduce the residence time of solid particles in the machine and increase the water content of discharged solids. Generally, the minimum differential speed of domestic equipment is several revolutions per minute, only a few manufacturers can reach 0.5r/min, while the minimum differential speed of foreign equipment can reach 0.2r/min, with a difference of more than 10 times, that is, the retention time of filter cake can be increased by more than 10 times.
(5) During the operation of the horizontal screw centrifuge, the movement of the filter cake on the drum surface is achieved by the relative movement of the screw generated by the differential to the drum. Since the speed difference between the drum and the screw of the horizontal screw centrifuge is small and the torque is large, the greater the output, the greater the torque of the screw conveyor, as shown in Figure 2.
Due to the high speed of the differential, the torque to be transmitted is large, and the lubrication conditions are poor. When the torque reaches a certain value, the life of the differential is greatly affected. Therefore, the clearance adjustment requirements for each part during the assembly process are particularly high, and the tolerance requirements are very precise. Too large or too small clearance is not conducive to the operation of the differential. Generally, the differential adopts the epicyclic gear train structure, and the planetary cycloid needle wheel
The advantages of involute gear differential are small size, light weight, large transmission ratio, efficiency up to 90%~99%, and large bearing capacity. The differential structures adopted by domestic and foreign centrifuges are basically the same. Generally, they are double stage 2K-H, 3K and K-H-V planetary involute gear differentials, or the combination of planetary cycloid needle gear and involute gear differentials. Centrifuge manufacturers often need special design and processing. Many domestic manufacturers have tried to localize the differential mechanism. Some manufacturers' machining accuracy and some performances have basically reached the international level. But on the whole, there is still a gap, especially in assembly accuracy and assembly experience. In addition, the main components are made of improper materials or restricted by material quality, The differential often fails to meet the design requirements, with low efficiency and short service life. Therefore, the key of domestic differential is not only the manufacturing quality, but also the assembly quality and material selection.
3、 Physical and chemical property parameters of materials
The physical and chemical properties of materials in the production process must be carefully and carefully selected in the selection of horizontal spiral sedimentation centrifuge. The machine performance is not affected by incomplete consideration of physical and chemical properties of materials. For example, some machines often suffer from torsional vibration, resulting in excessive vibration of the main bearing or action of the overload protection device. Physical and chemical parameters of materials include particle size, shape, property, density difference between solid and liquid phase, viscosity, etc. When the structural parameters of the centrifuge are determined, the production capacity of the centrifuge depends on the physical properties of materials and chemical operation conditions. According to the following formula, it can be judged:
In the process of separation, the greater the particle settling velocity VR, the more significant the separation effect; The smaller the particle diameter is, the slower the sedimentation speed is, and the more difficult it is to separate. The solid content in the centrifugal mother liquor also increases accordingly. On the contrary, the larger the particle diameter is, the faster the sedimentation speed is, and the easier it is to separate. The solid content in the centrifugal mother liquor is less, as shown in Figure 3. With the increase of density difference between solid and liquid phases, the greater the particle sedimentation velocity VR, the more significant the separation effect, and the less moisture content of filter cake, as shown in Figure 4. The viscosity of the suspension depends on the viscosity of the liquid phase and the concentration of the suspension. The smaller the viscosity, the greater the particle settling speed VR, and the more significant the separation effect; Judging from the following formula:
4、 Routing
The separation requirements of the horizontal spiral sedimentation centrifuge are determined according to the process route of the enterprise, and are restricted and affected by the pressure and temperature of the suspension at the feed inlet, the concentration and uniformity of the suspension, and the depth of the drum liquid pool.
(1) The influence of feed pressure on separation requirements In many production processes, the material level difference of high level tank is generally used to enter the centrifuge, and the feed pressure always changes. The change of feed pressure leads to the non-uniformity of feed, which can be adapted to the filter centrifuge, but is unfavorable to the horizontal screw sedimentation centrifuge. Especially when the feed pressure suddenly increases and the remote control valve lags behind, a large number of materials enter the machine, which will cause the feed pipe to be twisted and the inner cavity of the screw conveyor to be blocked, the machine will be unbalanced, the main bearing vibration will increase, and the machine will be seriously damaged if it is not handled in time. Therefore, the traditional feeding process has been abandoned and replaced by the pump feeding quantitative transportation process in large-scale equipment at home and abroad.
(2) Influence of feed temperature on separation requirements Increase of material temperature can reduce the viscosity of suspension μ, viscosity μ The decrease of can increase the particle settling speed VR, which can be seen from formula (1) to increase the separation capacity of the centrifuge. However, if the temperature is too high, the bearing and seal of the machine will be affected and the resistance of the auger will be increased, so the feeding temperature should be appropriate.
(3) The influence of feed concentration and uniformity on separation requirements Because the solid-liquid in the suspension is easy to delaminate, and the concentration of the material in the feed chute is uneven, although a mixing device is added in the feed chute, the material concentration becomes thicker at the bottom of the feed chute or at the end of the discharge, which is also easy to cause the machine to produce unbalanced force, and sediment blockage occurs in the feed pipe and spiral conveyor, As a result, the feed pipe is twisted and the machine is seriously damaged. Therefore, make-up water is often added to the inlet pipeline of the centrifuge. The design of the mixing device of the material tank strives to ensure that the materials are even. The capacity of the delivery pump should ensure that certain materials return to the material tank.
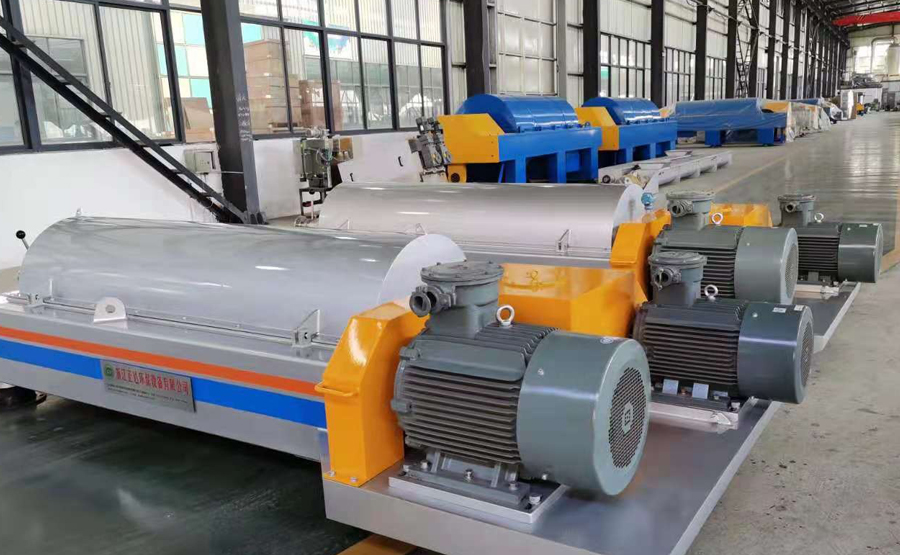
(4) The influence of the depth of the liquid pool of the drum on the separation requirements Adjust the weir plate at the outlet of the centrifugal mother liquid to adjust the depth of the liquid pool h. The deeper the pool, the shorter the length of the dehydration zone, the greater the moisture content of the product, and the smaller the solid content of the mother liquor. On the contrary, the moisture content of the product decreases, and the solid content of the mother liquor increases. Under certain separation factors, different machines have different lengths of dehydration zones. The moisture content of filter cake and the solid content of mother liquid can meet the best process requirements according to the liquid pool depth of the drum. Engineering technicians can reasonably select the liquid pool depth of the drum according to the post-treatment production conditions.
5、 Conclusion
In the actual production application, the selection of centrifuge is related to the success of the project. The reasonable model is selected, so that the energy consumption is reduced, the control is simple, and the product quality is high; Improper selection of model makes production impossible and causes great economic losses. In recent decades of development, Horizontal spiral sedimentation centrifuge Great changes have taken place in the structure, performance and parameters. The separation quality and production capacity have also been greatly improved, and the scope of application is also expanding. In particular, domestic industrial and mining enterprises are faced with huge pressure of energy conservation and emission reduction. In terms of enterprise sewage treatment, sludge dewatering is a key technology, and the decanter centrifuge has many advantages such as automatic, efficient, airtight and continuous, which plays a significant role in this key technology.
Zhejiang Zhengda Environmental Protection Equipment Co., Ltd.: focusing on Horizontal spiral sedimentation centrifuge, sludge dewatering machine, sludge treatment equipment, centrifugal dewatering machine, sludge dewatering equipment, solid-liquid separation equipment, horizontal spiral centrifuge, centrifuge, mud dewatering machine, mud dewatering equipment, mud treatment equipment, horizontal centrifuge, solid-liquid separator Production, sales and service of various solid-liquid separation equipment. Welcome new and old customers to come for consultation and investigation.
Factory address: No. 812, Jiulong Street, Bihu Town Industrial Zone, Liandu District, Lishui City, Zhejiang Province Telephone: 0578-2788008 Fax :0578-2788681
Email: [email protected] website: //hcsxe.com
Mobile: 15857812218 (Mr. Mao) fifteen billion two hundred and fifty-seven million eight hundred and twenty-six thousand six hundred and nine (Manager Xu) thirteen billion nine hundred and six million seven hundred and eighty-eight thousand three hundred and sixty-seven (Mr. Xu)