according to Horizontal screw centrifuge According to the characteristics of wear failure, it is proposed to adopt laser surfacing technology on the working face of spiral blades, explore a suitable surfacing technology, and obtain a high-performance surfacing layer with metallurgical bonding with the matrix and uniform and refined microstructure change. The analysis shows that the hardness and wear resistance of laser surfacing layer are increased by 2 times and 5 times respectively, and the corrosion resistance meets the application requirements. This technology is used for horizontal snails Centrifuge The blade has high practical value.
Most of the traditional measures to improve blade wear are welding blade liners of different materials, spray welding hard materials or inlaying alo ceramic liners. Because spray welding often has problems such as low bonding strength, porosity, non compact structure, uneven composition, large deformation of blade, etc; However, the ceramic chip inlay also has a poor bonding between the lining and the substrate, which is easy to fall off when the centrifuge rotates at high speed, resulting in accidents, and it is difficult to meet the working conditions of the horizontal screw centrifuge. Therefore, according to the design and working characteristics of horizontal screw centrifuge, we studied the laser surfacing strengthening of stainless steel used horizontal screw centrifuge blades in corrosion resistant environment, and achieved good application results. stainless steel; Surfacing material: ti alloy solder for laser. The preset laser surfacing method is used to obtain a single bead surfacing layer each time, and there is a gap between each bead, so as to avoid the thermal impact between processes. A 7 kw transverse flow co_2 laser was used; The output power of the laser is 2.8 kw and 3.0 kw respectively; The output laser beam spot diameter is 7 mm. Laser surfacing of stainless steel is a complex process of metallurgy and crystallization. Due to the high speed of laser heating and melting cooling, uneven temperature field and thermal stress are formed between the microstructure of materials during heating, cooling or melting condensation, which is easy to cause defects such as crystal cracking and cracks. In order to obtain good quality of the surfacing layer (such as smooth surface of the surfacing layer, no cracks, good metallurgical bonding, etc.), it is necessary to adjust the relevant laser process parameters (laser energy density, scanning speed) to form a good match, and carry out sample simulation wear experiments and corrosion resistance tests to obtain good laser process parameters to make it have a good match performance.
The samples were cut by wire cutting, and prepared by electrolytic polishing and electrolytic corrosion. Measure the change of hardness along the width and depth on the surface in the direction perpendicular to the scanning direction. Vickers hardness value (200g15s) is used to represent the result of hardness measurement.
3 Test results and discussion
In order to describe the influence of process parameters, the energy density of laser action pw=p/(× 2a) and the action time t=2d/v are introduced,. Where p is the laser output power; Is the scanning speed; D is the beam radius. Select different process parameters for experimental study.
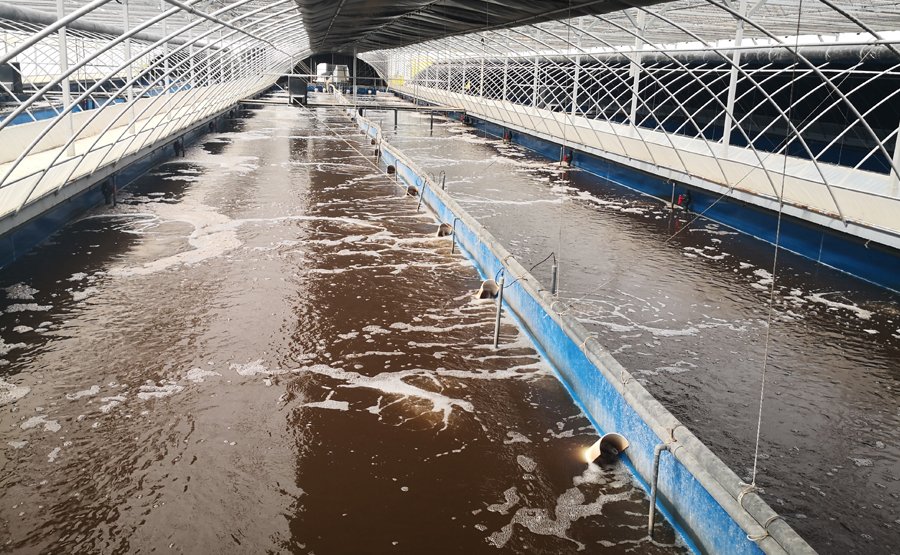
3.1 Microhardness
After laser surfacing, higher hardness value can be obtained than other methods. Figures 1 and 2 respectively show the variation rules between different laser process parameters. As shown in Figure 1, the hardness of surfacing alloy on stainless steel is significantly improved, the average hardness of surfacing layer is hv400, the thickness of surfacing layer is 0.7~1mm, and the hardness of surfacing layer is in gradient transition. At the same speed, with the increase of laser power, the microhardness of the surfacing layer also increases, which is determined by the extremely fast speed of laser heating and cooling. The microhardness curves at the same power and different speeds are shown in Figure 2. When increasing, the hardness of the surfacing layer decreases, the energy absorbed per unit volume decreases, and the thickness of the surfacing layer decreases. Figure 2 also clearly verifies this point, which also shows that under the experimental conditions, the structure of the typical stainless steel surfacing coating with energy density playing a leading role is shown in Figure 3, the junction surface is relatively flat, and the transition zone between the matrix and the surfacing layer presents columnar and dendritic crystal structures, and the representative microstructure is shown in Figure 4. The heat dissipation in the process of surfacing crystallization includes two aspects: the high temperature radiation from the surfacing pool to the space and the heat conduction through the collective material. Because the weld pool is small and the base material is large, the cooling rate of the base to the weld pool is very fast. Therefore, the crystal growth is equivalent to directional solidification, which leads to the development of columnar crystals when the surfacing layer crystallizes. At the same time, new crystals are nucleated on the surface of the molten pool due to high temperature radiation. The bottom of the surfacing layer belongs to the typical plane epitaxial growth structure, and the dendrite structure is coarse; However, the top of the surfacing layer is a regular dendritic eutectic structure and the dendrite is smaller than that, which means that columnar crystals and dendritic crystals appear alternately, which is conducive to increasing the bonding strength of the surfacing layer (as shown in Figure 4). When the laser processing parameters are not suitable, the defects such as pores and inclusions are easy to appear.
Zhejiang Zhengda Environmental Protection Equipment Co., Ltd.: focusing on Horizontal spiral sedimentation centrifuge, sludge dewatering machine, sludge treatment equipment, centrifugal dewatering machine, sludge dewatering equipment, solid-liquid separation equipment, horizontal spiral centrifuge, centrifuge, mud dewatering machine, mud dewatering equipment, mud treatment equipment, horizontal centrifuge, solid-liquid separator Production, sales and service of various solid-liquid separation equipment. Welcome new and old customers to come for consultation and investigation.
Factory address: No. 812, Jiulong Street, Bihu Town Industrial Zone, Liandu District, Lishui City, Zhejiang Province Telephone: 0578-2788008 Fax :0578-2788681
Email: [email protected] website: //hcsxe.com
Mobile: 15857812218 (Mr. Mao) fifteen billion two hundred and fifty-seven million eight hundred and twenty-six thousand six hundred and nine (Manager Xu) thirteen billion nine hundred and six million seven hundred and eighty-eight thousand three hundred and sixty-seven (Mr. Xu)