Solid liquid separation technology It is a widely used technology, which is suitable for medicine, chemical industry, metallurgy, textile, environmental protection, food and other industries. It is a kind of equipment that uses centrifugal force as the driving force to achieve different separation purposes according to the physical characteristics and separation requirements of suspensions or emulsions such as liquid-solid, liquid-liquid or liquid-liquid solid. Because of its simple structure and high efficiency, Pure physical separation process can fully guarantee the characteristics of separated materials. Therefore, Centrifuge Its market application is extremely extensive.
In recent years, China's national economy has continued to develop, new technologies and new processes have emerged, and the application of centrifuges has become more extensive; However, in this process, most manufacturers are more concerned about the separation performance and strength requirements of centrifuges, and often pay less attention to the impact of corrosion factors, which has brought some negative effects,
1、 Centrifuge environment Centrifuges are divided into different types of equipment according to function and structure, but they all have common characteristics
2、 Possible corrosion
Metal corrosion forms are mainly divided into two categories: uniform corrosion and local corrosion. The former is easy to find because of its apparent phenomenon, and it is clearly described in most manual data. I will not elaborate here, but only discuss the latter. Local corrosion only occurs locally, which is an extremely serious and harmful damage, such as pitting corrosion, crevice corrosion, intergranular corrosion, stress corrosion, wear corrosion, etc. In centrifuges, local corrosion is widespread, and its formation mechanism should be analyzed emphatically, and measures should be taken to overcome it.
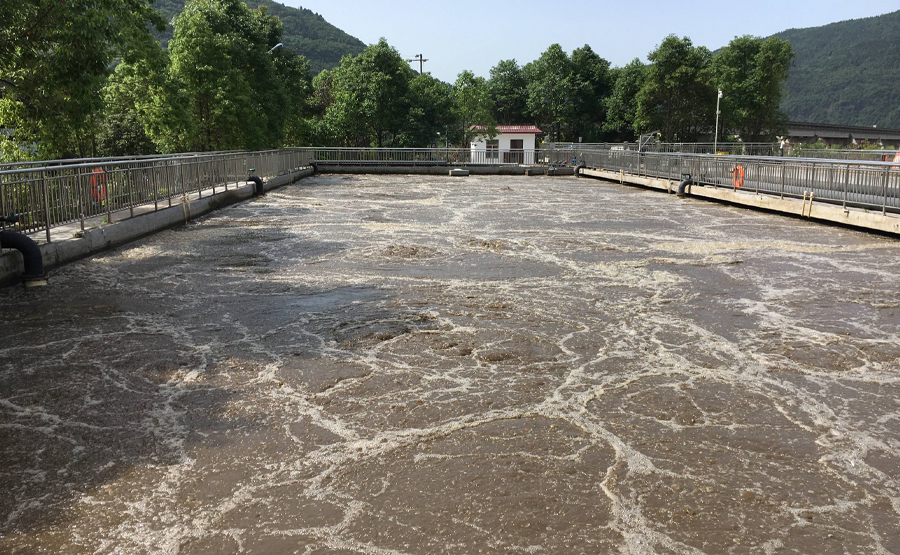
1. Pitting corrosion is a highly corrosive phenomenon, which mainly exists in metals that are easy to passivate, such as stainless steel. Due to the possible defects on the surface and the presence of active ions in the solution that can destroy the passive film, the passive film is partially destroyed, thus forming a couple, causing pitting corrosion. After the formation of pitting, due to the effect of centrifugal force, the dynamic process of galvanic couple in the hole will be accelerated, so as to ensure the continuity of pitting corrosion until perforation, which is different from the pitting phenomenon in static state.
2. The intergranular corrosion will cause the loss of strength and extensibility of the parts and cause brittle fracture of the parts. It is a kind of harmful damage that develops from the surface along the grain boundary to the inside and has no signs of corrosion on the outer surface.
3. Wear corrosion means that the surface of parts is subject to wear and corrosion damage at the same time.
4. Stress corrosion is the damage caused by certain tensile stress in corrosive environment. It has the following characteristics: residual tensile stress, external tensile stress, corrosive infiltration environment, local defects. The above four kinds of corrosion have extremely serious impact on the machine, which may lead to serious consequences.
3、 Measures
1. Different models are required for different materials and separation requirements. After the model and main parameters are determined, the strength part materials are determined from the basic aspects according to the corrosion resistance of different materials in different environments, their physical and chemical characteristics, cost performance and other factors. From the material itself, the target material is safe.
2. Structural design
An excellent design can extend the service life of the equipment and ensure the safety of the equipment. For structural design, the design defects that are most likely to accelerate corrosion are stress concentration tendency and crevice environment. Sometimes, although the corrosion rate is small in the metal immersion solution; However, the formation of crevices will cause serious crevice corrosion due to changes in the chemical and electrochemical state of the internal solution,
3. Surface protection measures
One of the basic ideas for corrosion control is to isolate the corrosive environment. In centrifuge design, surface treatment methods, such as flange, galvanizing, chrome plating, chemical coating, etc., are often used. These methods are effective in many environments. However, for rotating parts, an important phenomenon must be noted: the base material and coating are two kinds of materials, and their linear expansion coefficients are different, which will produce different deformation when the rotating parts undergo elastic deformation, So as to produce a large number of microcracks; If the above phenomenon exists, it will accelerate the formation of corrosion. Therefore, for
The surface protection method of rotating parts shall be carefully adopted.
4. Corrosion inhibitor
The centrifuge itself involves many disciplines. In addition to the above measures, we should also pay attention to the research of its application environment in order to use the centrifuge well. Corrosion inhibitors are also widely used in practical applications. For some harsh environments, the use of appropriate corrosion inhibitor can make the parts applicable. As long as the process permits, the use of corrosion inhibitor should be an effective way for centrifuge application.
3、 Select which type of separation equipment.
The separation equipment used in heavy oil separation industry is mainly divided into: full slag removal type and partial slag removal type separation equipment according to the slag removal type; According to the type of separated materials, it can be divided into miscellaneous type and water separation type.
Generally speaking, the selection of models is inconsistent: the customer's requirements for separation equipment are mainly to remove impurities from heavy oil, so for heavy oil with high mechanical impurities and water content less than 3%, the separation equipment that ensures slag removal shall be selected first, that is, during the separation process, the slag removal performance of the separation equipment shall be adjusted to ensure slag removal
The slag is maximized, while the removal of water is relatively unimportant. If the water content of heavy oil is more than 3%, another drainage separation equipment must be considered at the same time, or the corresponding adjustment should focus on the removal of water in the oil. Otherwise, it is likely to cause power generation failure of lower level diesel engines, such as load shedding. Selection of treatment capacity: generally speaking, when burning heavy oil, the exhaust temperature of diesel engine is 15~20'12 higher than that when burning light diesel oil, and the fuel consumption rate is about 5%~8% higher. Therefore, when you know the rated capacity of the diesel engine, you will know how much the separation equipment with rated capacity is required to be applicable.
In addition, it should be noted that the user should inquire clearly in advance about the indicators of oil used, confirm the corrosivity of the materials, and indicate them to avoid disputes.
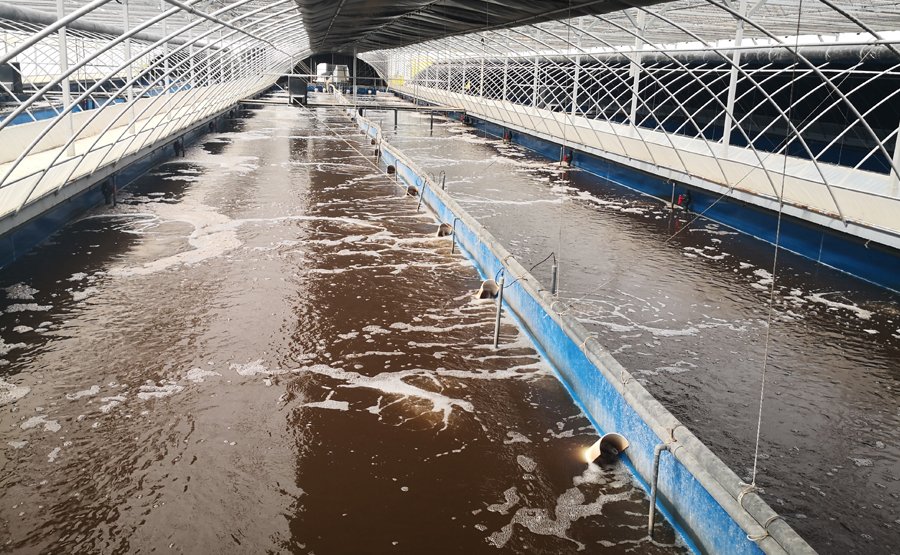
4、 How to better use the separation equipment Due to the characteristics of heavy oil itself, when separating materials, the mechanical part will be corroded, including cold corrosion and hot corrosion. When the heavy oil is running in the separation equipment, due to the high required separation temperature of the heavy oil, the sulfur in the heavy oil will produce a certain amount of sulfuric acid and sulfite, which will condense on the surface of the parts after shutdown, forming cold corrosion; High temperature of heavy oil will also lead to hot corrosion of vanadium and sodium compounds on materials directly. In heavy oil separation, hot corrosion has more serious consequences than cold corrosion. In order to prevent the above situations from occurring in large numbers, lowering the temperature will affect the separation effect. Therefore, there are only two solutions at present: one is to adjust the separation temperature according to the actual material situation, which is generally controlled at about 60 ℃~75'12. The premise of this method is that the slag content of the material is relatively small and the viscosity is low. Another method is to change the material in contact with the material in the separation equipment according to the material situation. The above is my understanding of the heavy oil separation industry, as well as the recommendation and use of the corresponding models of heavy oil separation. Inappropriate welding, unreasonable heat treatment and uneven force of fastening bolts will cause local stress concentration. Therefore, finding the correct processing method is also an effective way to prevent corrosion. The corrosion problem of centrifuge is a comprehensive and complex problem, because the working environment of centrifuge is quite different from the data obtained in the general information manual in static state. Therefore, when referring to relevant data, in addition to the above analysis, the influence of many factors such as dissolved oxygen in solution, temperature, high-speed fluid and flow state change in the separation area should also be considered, and appropriate measures should be taken to ensure the safe and reliable operation of the centrifuge.
Zhejiang Zhengda Environmental Protection Equipment Co., Ltd.: focusing on Horizontal spiral sedimentation centrifuge, sludge dewatering machine, sludge treatment equipment, centrifugal dewatering machine, sludge dewatering equipment, solid-liquid separation equipment, horizontal spiral centrifuge, centrifuge, mud dewatering machine, mud dewatering equipment, mud treatment equipment, horizontal centrifuge, solid-liquid separator Production, sales and service of various solid-liquid separation equipment. Welcome new and old customers to come for consultation and investigation.
Factory address: No. 812, Jiulong Street, Bihu Town Industrial Zone, Liandu District, Lishui City, Zhejiang Province Telephone: 0578-2788008 Fax :0578-2788681
Email: [email protected] website: //hcsxe.com
Mobile: 15857812218 (Mr. Mao) fifteen billion two hundred and fifty-seven million eight hundred and twenty-six thousand six hundred and nine (Manager Xu) thirteen billion nine hundred and six million seven hundred and eighty-eight thousand three hundred and sixty-seven (Mr. Xu)